Concrete: it’s all around us. It makes up sidewalks, buildings, pavements, bridges, and dams, and can be shaped (within reason) to a builder’s whims. The ubiquitous material probably escapes everyday notice simply because it is everywhere. So, is concrete really a big deal?
“I have a presentation that starts out asking that question,” says Fred Aguayo, an assistant professor with the Department of Construction Management at UW’s College of Built Environments. “People see concrete science and engineering and think it’s not really a major thing: You mix rocks, sand, and water, and you have a hardened product at the end of the day. But, that’s not the whole story.”
Concrete recipes and ingredients can change how the material performs, the subject of Aguayo’s research. His research has major implications for carbon sequestration, climate change, and the construction industry. It also means that concrete has a secret life you’d never guess at by just glancing at a building or walking a city sidewalk.
Generally speaking, concrete is made by mixing cement with aggregates (sand and rocks), often chunks of granite. Cement is the secret sauce, a kind of binder that holds the whole mixture together.
The material has a long and respectable history. The World Cement Association notes that cement has been used for over 10,000 years. Romans added sand, crushed rock, bricks, tiles, and ceramic shards to lime and volcanic ash to construct long-lasting buildings and roads.
According to Daniel Akerele, Aguayo’s first-year Ph.D. student in the CBE’s Department of Construction Management, there’s some intense chemistry in producing cement. First, limestone is heated to around 1500 degrees Celsius, producing quick lime, or calcium oxide (CaO). Quick lime is mixed with other raw materials (including iron, silica, alumina, and gypsum), ground to a powder, and mixed with water, undergoing a chemical reaction to calcium hydroxide (Ca[OH2]) and calcium silicate hydrate, the glue of the material. It’s combined with fine and coarse aggregates, and gradually hardens and develops the mechanical strength needed for concrete.
Aguayo caught the concrete “bug” as an undergraduate student at the University of Texas-Austin (UT), and never looked back. “My main areas of research are concrete durability and sustainability, and also developing methods to identify how different materials form and predict those performances in real-world structures,” says Aguayo. Essentially, he’s a concrete chemist with a penchant for practical applications.
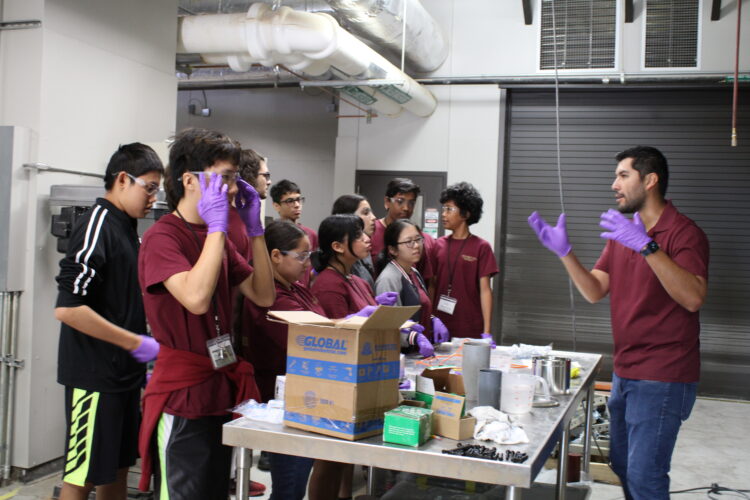
His graduate student, Akerele, has a background in civil engineering and seven years of experience as a construction manager in Nigeria. When he decided to enter academia and began searching for an advisor, he ran across Aguayo and appreciated the professor’s novel research. “My research at UW focuses on concrete carbonation, alternative cement additives for structural applications, and sustainable construction,” he explains.
Concrete applications for the material world
Concrete can be quite porous, which means that water (along with other deleterious chemicals) can permeate concrete, speeding up its deterioration. Aguayo is interested in understanding how this mechanism progresses in different cement-based materials, and identifying ways to give concrete structures a longer life.
Take sulfates, for example: salts derived from sulfuric acid that are found naturally in certain types of rocks. They’re present in soils and groundwater, and found in detergents, shampoos, fertilizers, and industrial wastewater. Sulfates in soil can slowly corrode concrete that’s in contact with it.
“Imagine a concrete bridge deck being cast and placed,” says Aguayo. “Concrete inevitably wants to shrink and move, and in this case, there are a lot of restraints on that movement.” The tension will eventually cause cracking, introducing moisture and sulfates that can corrode the structure. “For the past four or five years, I’ve been researching these durability issues with the application of newer, alternative-based cements.”
Extending the durability and lifespan of concrete products will also reduce Co2 emissions. As Aguayo explains, concrete production is one of the biggest sources of carbon dioxide emissions in the world, simply because we use so much of it. Part of his research, as well as Akerele’s, is testing out concrete recipes to yield longer-lasting products.
Portland cement—similar to the substance used in Roman times—is the most widely used cement today, with cheap and regularly available components. “The disadvantage is that it emits a lot of Co2 during production,” says Akerele. That’s a big deal: burning limestone and producing cement is the second-largest contributor to carbon emissions.
If Portland cement isn’t the most durable material, what kind of binder should we be using to hold the fabric of our built environments together?
Smashing rocks in the concrete lab
Aguayo joined the UW faculty in fall of 2021, and started working on campus in January 2022. He and Akerele are building out a new concrete materials lab. “As one of the only experts at UW focusing on researching concrete at the material science level, I’m excited to build a lab that capable of testing and characterizing advanced materials to achieve the goal of a safer, durable, and sustainable infrastructure,” explains Aguayo.
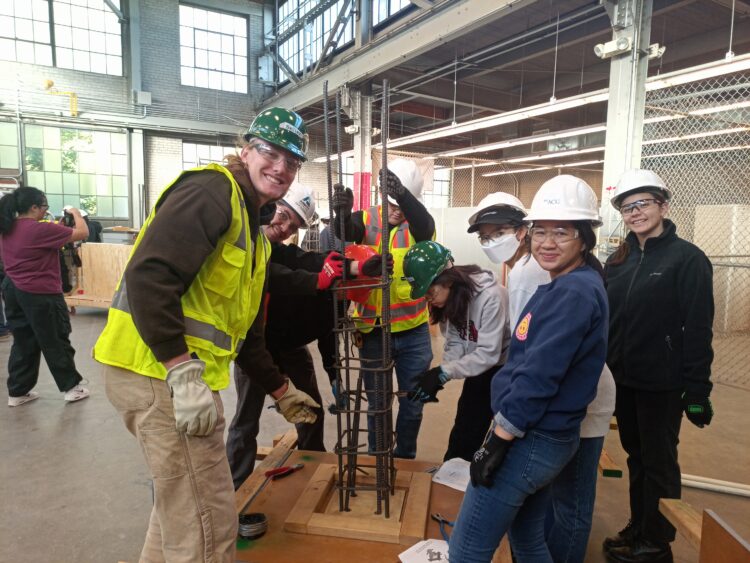
Aguayo hopes to attract an “army” of students to his new lab. This probably won’t be difficult, as Akerele describes Aguayo as a down-to-earth mentor invested in student success. “I couldn’t have asked for a better supervisor,” he reports.
What innovations are they researching? Aguayo experiments with cement alternatives. One alternative replaces up to 15 percent of a project’s cement with ground limestone, yielding a product called Portland limestone cement (PLC) and reducing the greenhouse gases emitted by burning limestone. Concrete can be made even more sustainable by diverting waste materials—fly ash, slag, and silica fume—from landfills and using them as a concrete additives.
Other alternatives include calcium aluminate and calcium sulfoaluminate cements. These materials set rapidly, develop strength much faster, and have the potential to reduce concrete shrinking or cracking. Placing concrete with quick-drying cements requires more planning time for construction crews. But, the potential benefits outweigh the hassle.
“Imagine trying to perform construction work in Seattle on the I-5 corridor,” says Aguayo. “You need this to be done quickly, otherwise you have significant costs and disruptions to the public. You also need to use durable materials so the repairs last for a significant amount of time.”
Infrastructure repairs can be completed at a rapid pace by replacing Portland cement with calcium sulfoaluminate (CSA) cement in the concrete mixture. With a potential project to restore deteriorating bridge decks in the works for Aguayo, CSA cement may come in handy.
Another incredible property of the material is that it sequesters carbon, otherwise known as cement carbonation. Akerele says that in some cases cement can sequester around half the carbon produced during its manufacture. CSA cement not only emits less Co2 during production, it also carbonates faster than some other types of cement. Akerele is working to find out if the accelerated carbonation process affects CSA cement’s other properties.
Despite advancements in concrete materials and performance, not a lot has changed for contractors. Portland limestone cement has been around since around 2005, but it’s only recently gained traction as a construction material.
Akerele’s research advances an understanding of barriers to innovation in cement and concrete performance among contractors. “The construction industry is less risk receptive than most other industries,” he says. “So, how do we help them accept these innovative technologies? Is it a regulatory issue? Do they not have enough information? Is it the cost?” Akerele hopes to determine the answers to those questions.
It’s not enough to get contractors excited about concrete innovation. Aguayo wants students to understand that construction materials can be just as exciting as the building process.
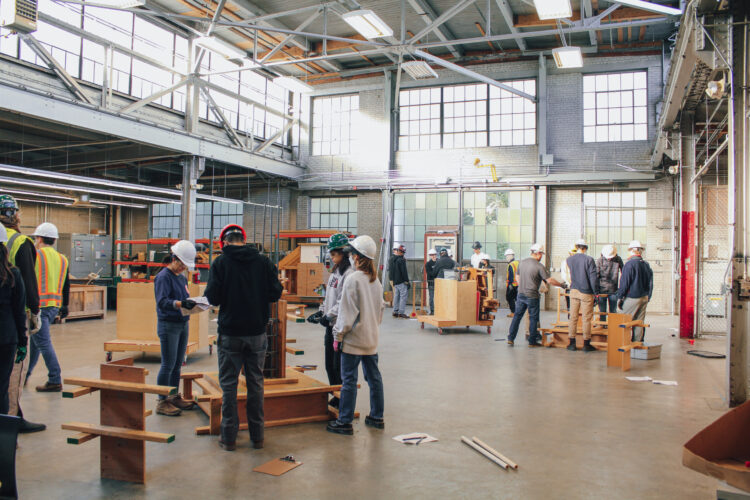
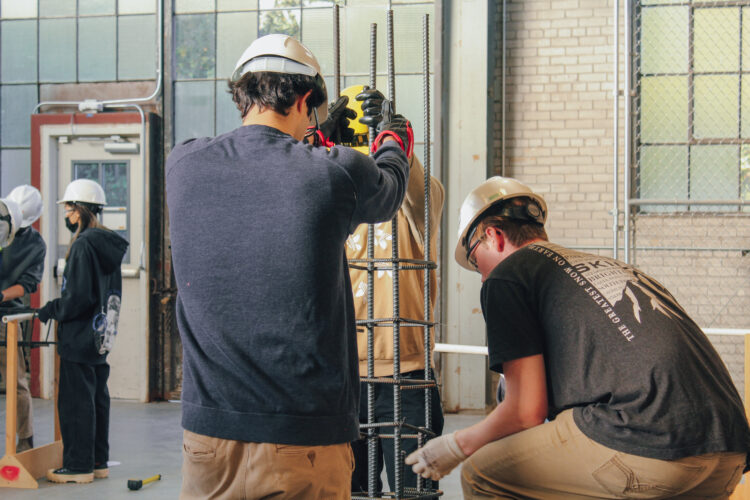
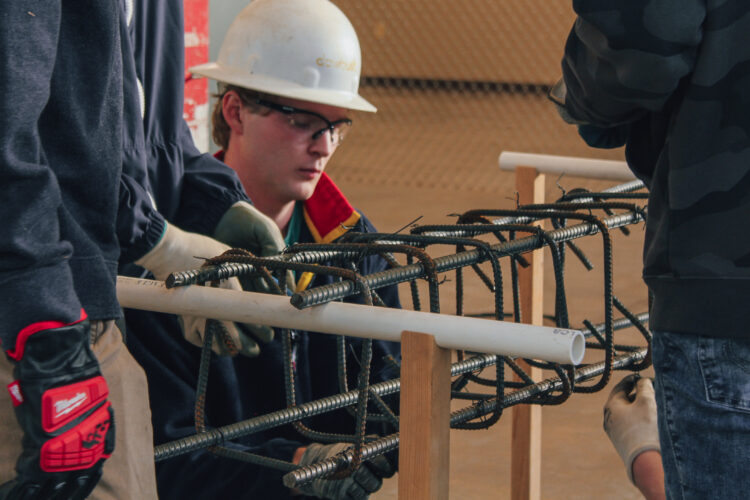
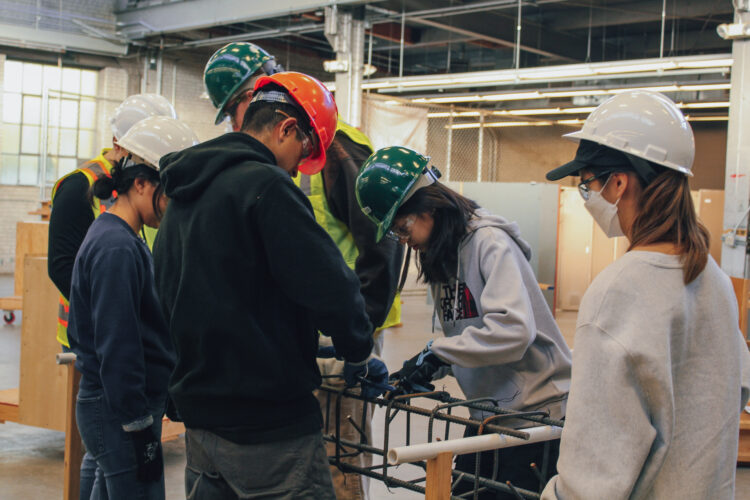
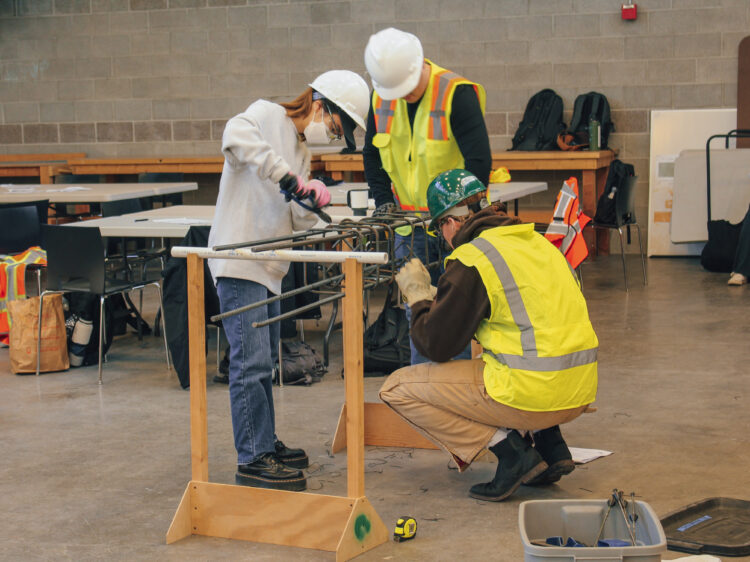
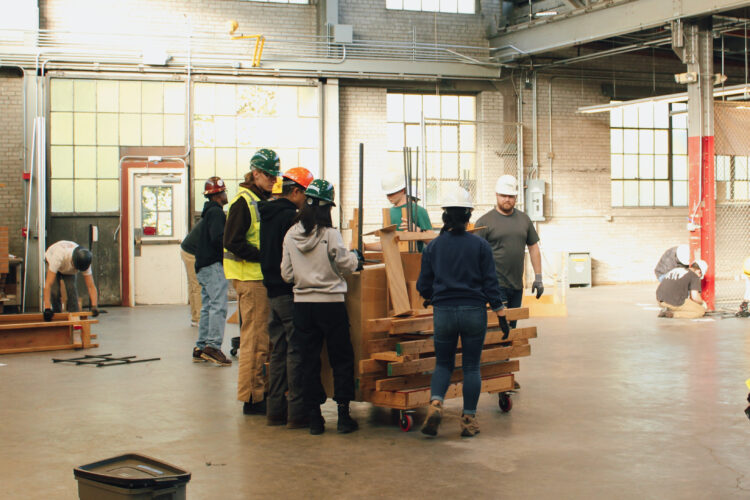
“One of the things I always say when I’m interviewing students is that we’re not a white-coat lab,” says Aguayo. Students are wearing safety glasses and latex gloves, cranking out concrete in a drum mixer and understanding how it holds up under duress. They get a resumé boost and real hands-on experience: Aguayo plans on taking students into the field to get a sense of the assessment process. Former students have gone on to become contractors, engineers, consultants, and concrete manufacturers.
“What you see on the outside is just this gray material mixed with water to make strong structures, but underneath that there’s a lot going on. That’s the science that I really fell in love with.” If there’s anyone who can convince students to love the magical chemistry of cement and concrete, it’s Fred Aguayo.
By Jen DeMoss. Jen is a freelance writer based in Michigan.